Back in 2018 when I got the CupCake out to fix the extruder-stall problem from 2014, it had a new problem of the Z motor not doing what it was asked. The stalling motor was enough to stall me for another couple of years; or was the skipping motor enough to cause me to skip ahead to 2020 for further diagnosis?
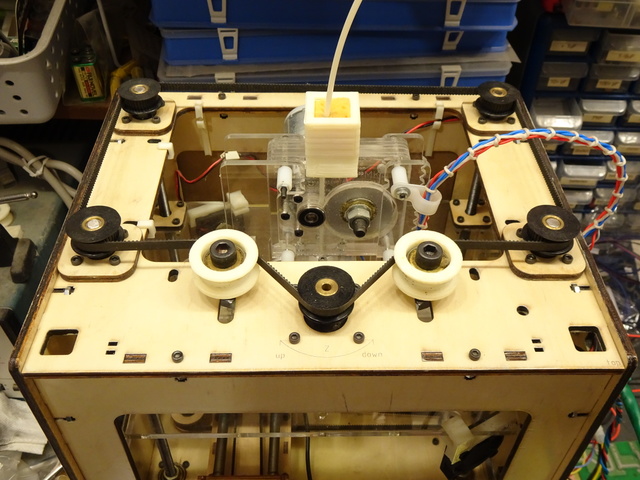
The CupCake’s extruder mounts on a Z stage that lowers down to the build platform. The Z axis is run by a stepper mounted inside the frame at the front, with the central black pulley on the motor shaft driving the belt that connects the four black pulleys on threaded rods protruding down into the machine to raise and lower the Z stage by its corners.
As I was testing in 2018, and again this spring, what should have been continuous movement of the Z axis getting down to the platform to start a print would once in a great while pause and resume. I didn’t hear the characteristic clack/clonk of a stepper motor skipping steps, but it was hard to be sure. But whatever the cause, if the Z motor wasn’t running completely reliably before a print, there’s a fair chance that it could misbehave during a print. Plus a printer with neither Z probe nor Z endstop makes it hard enough to set first layer height already; I don’t need to play this game in Nightmare mode.
Part of the challenge was replicating the problem. In the first run at Cort’s house, everything worked initially, then finally misbehaved many minutes into a print. After restarting the print, again it took many minutes before the next failure, suggesting that we were going to have a dickens of a time watching the problem on a scope and reinforcing my decision to take it to his house where we could use his digital scope with triggered capture.
However, after some fiddling, we discovered that if I used the ReplicatorG control panel to continually jog the Z up and down, at least after the printer was warmed up, it would occasionally pause, which we could hear as well as see. That in turn led to an even more interesting discovery.
Read the rest of this entry »